Las propiedades de las baldosas cerámicas vienen determinadas por la microestructura del material que, a su vez, depende de la naturaleza de las materias primas empleadas, así como de las distintas etapas que integran su proceso de fabricación. A través de estas etapas interconectadas, la mezcla inicial de materias primas experimenta una serie de transformaciones fisicoquímicas de forma progresiva, generándose diversos productos intermedios para, finalmente, dar lugar al producto final.
Esta mezcla de materias primas se somete a operaciones de molturación para garantizar una mezcla homogénea de sus componentes, con una distribución de tamaños de partícula adecuada, y debidamente acondicionada para el moldeo de la pieza. La molturación puede realizarse por vía seca o húmeda, siendo necesario en este último caso secar la suspensión resultante mediante atomización. Este es un proceso continuo y automático que permite obtener una serie de gránulos de material (polvo atomizado), con un contenido en humedad determinado y una forma y tamaño idóneos para que fluyan en la siguiente etapa del proceso cerámico: el conformado.
Durante el conformado, el polvo atomizado se vierte en un molde mediante un sistema de transporte para, seguidamente compactarlo y obtener la forma de la baldosa. En el moldeo de piezas planas, debido a su geometría sencilla y a la pequeña relación espesor/superficie, se realiza un prensado unidireccional en seco empleando, generalmente, prensas hidráulicas. De esta forma, se obtienen las baldosas en crudo que son trasladadas a un horno en el que tendrá lugar la etapa de cocción a alta temperatura.
A pesar de los importantes avances en los sistemas de prensado y en la tecnología de los hornos, curiosamente, la primera etapa de llenado del molde no ha experimentado apenas avances en las últimas décadas. En la actualidad, la precisión de esta etapa sigue dependiendo de la experiencia e intuición del operario, siendo esto especialmente relevante cuando se trata de fabricar baldosas de gran formato (mayores de 120 cm × 120 cm). Independientemente del mayor o menor grado de destreza del operario, este es un procedimiento que sigue siendo muy propenso a generar defectos en las baldosas debido a una ineficaz distribución del polvo en el molde. Así, según Tíscar et al. (2019), sigue faltando un enfoque científico y sistemático para mejorar esta etapa.
El método de los elementos discretos (DEM) simula numéricamente el comportamiento reológico de un medio formado por un conjunto de partículas, las cuales interaccionan entre sí a través de sus puntos de contacto. Por consiguiente, representa una metodología adecuada para el estudio de materiales granulares y discontinuos. Esta metodología se ha utilizado en el análisis del flujo de polvos durante la descarga de silos, la simulación de ensayos de compresión o en la mezcla y el transporte de polvos, entre otros.
Con esto, las simulaciones DEM suponen un enfoque computacional para comprender y optimizar el proceso de llenado de moldes que se emplean actualmente en la fabricación de las baldosas cerámicas. De esta manera, es posible analizar cómo se generan los defectos durante el conformado de baldosas cerámicas, así como proponer estrategias para su prevención.
Con esta premisa se desarrolló, junto con MACER S.L, un software de simulación de materiales granulares mediante el DEM, especialmente diseñado para resolver la problemática asociada al proceso de llenado de moldes en la fabricación de baldosas cerámicas. El éxito del software impulsó el desarrollo de una herramienta de simulación de polvo más generalista, denominada ScaleDEM, y desarrollada por ITC-AICE junto con la Universidad de Gante. Se trata de un software modular de simulación de materiales granulares en entornos industriales, que proporciona una mejor comprensión de los equipos de manipulación de polvo, así como la creación de prototipos virtuales.
La herramienta es lo suficientemente flexible para adaptarse a diversos entornos industriales en los que se manipulen materiales granulares, resolviendo las necesidades específicas de cada caso y garantizando la correlación entre los resultados de la simulación y la realidad de la planta de producción.
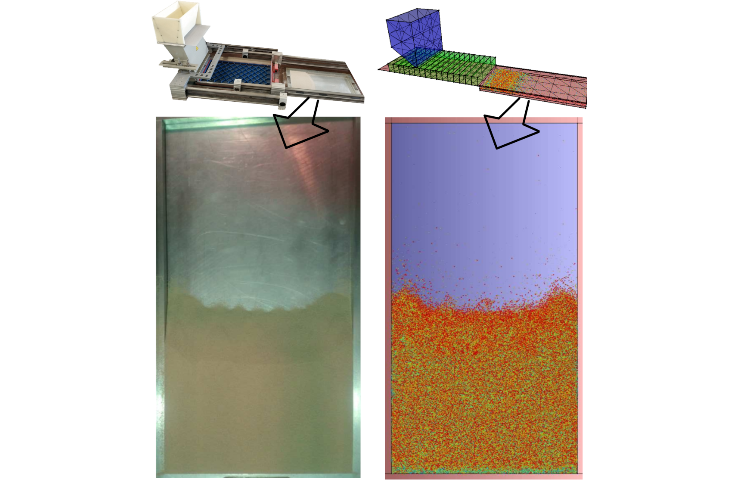